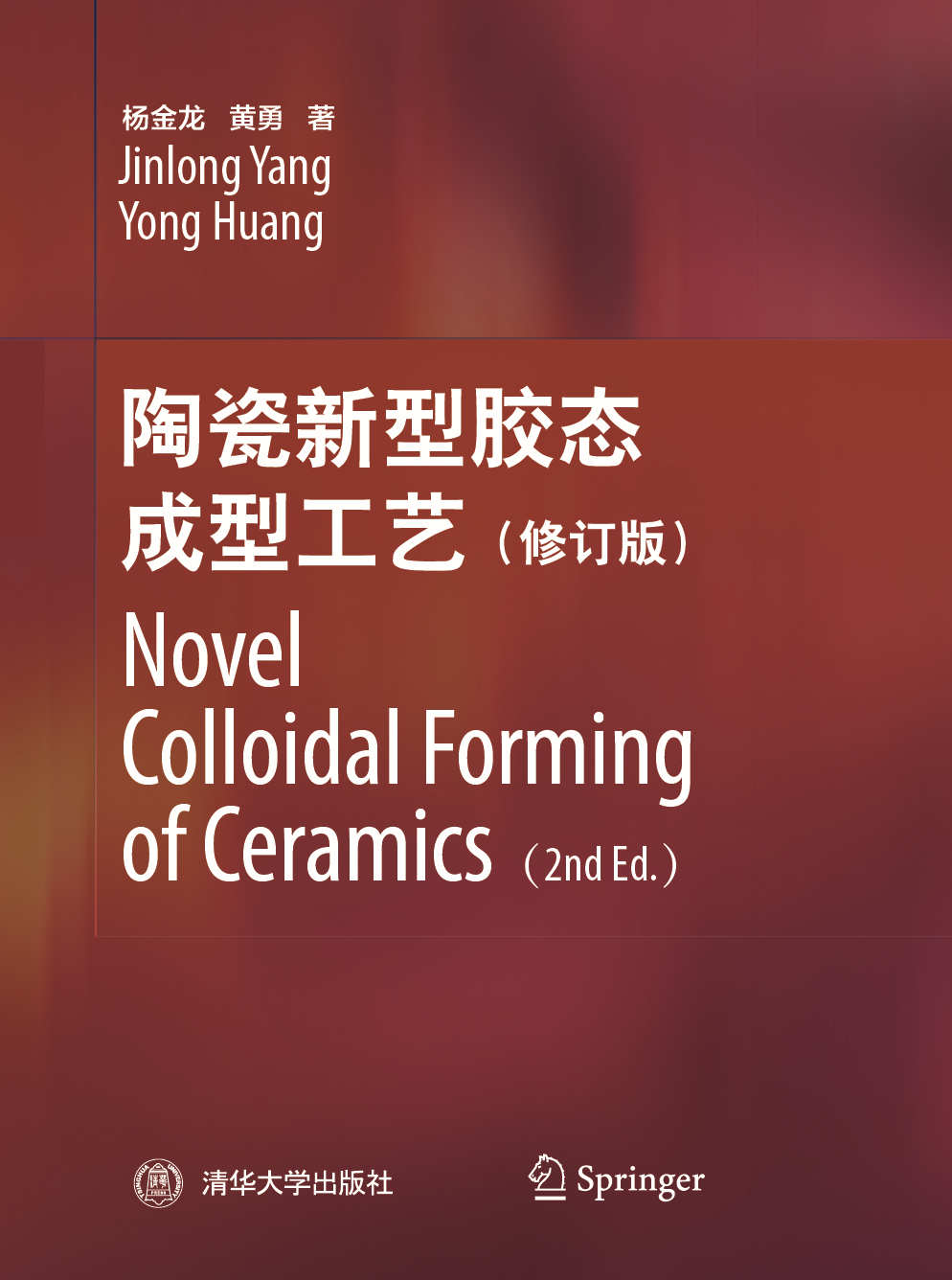
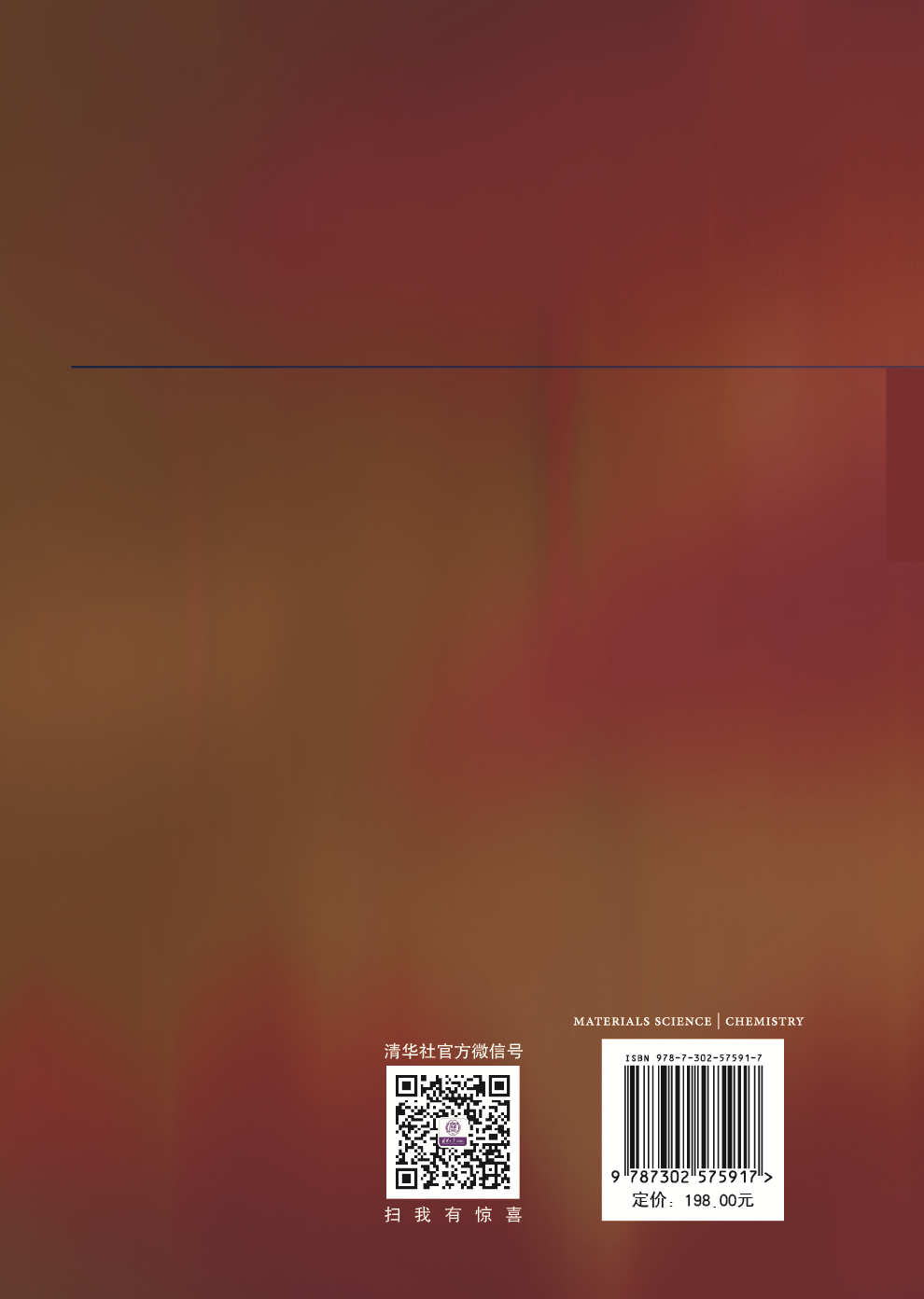
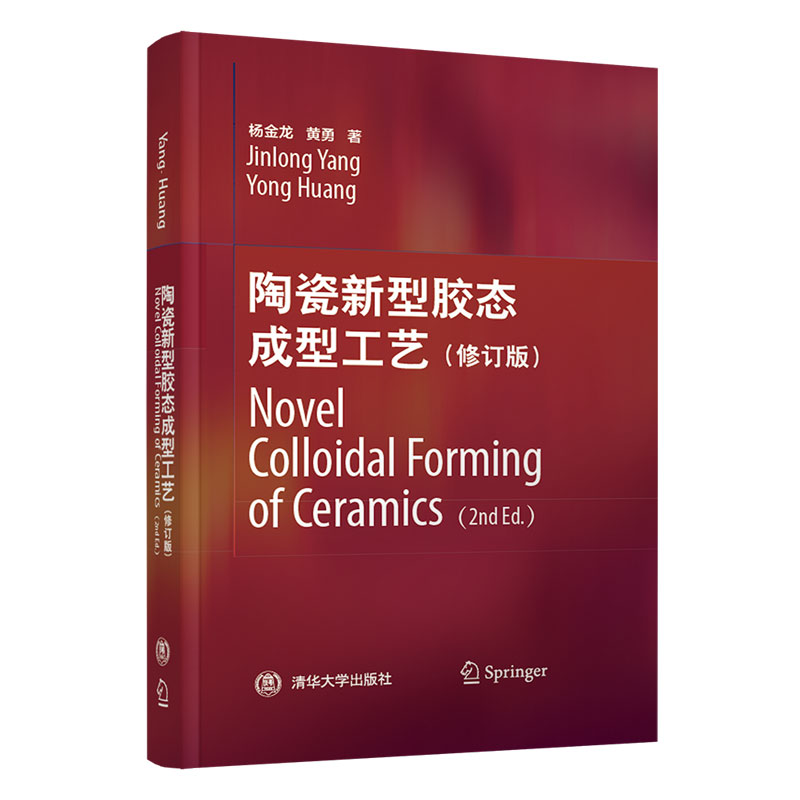
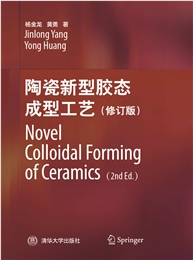

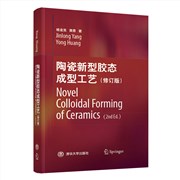
作者:杨金龙 黄勇 Jinlong Yang, Yong Huang
定价:198元
印次:2-1
ISBN:9787302575917
出版日期:2021.03.01
印刷日期:2021.03.03
图书责编:黎强
图书分类:学术专著
本书介绍了清华大学在高性能陶瓷成型工艺领域取得的研究成果和其他国家学者在该领域所取得的进展,内容包括:基于凝胶体系的陶瓷胶态注射成型新工艺;陶瓷基片的凝胶流延工艺;无毒或低毒体系凝胶成型工艺;陶瓷制备过程中缺陷产生、演化、遗传和控制;非氧化物陶瓷凝胶注模成型新工艺;胶态成型工艺的应用;悬浮体成型技术;胶态成型工艺新方法和新技术。
杨金龙教授,1966年5月出生于山西省太原市;1987年,毕业于北京理工大学金属材料及热处理专业,获得学士学位;1990年,毕业于中北大学金属材料及热处理专业,获得硕士学位;1996年,毕业于清华大学材料系无机非金属专业,获得博士学位。1999年5月-2000年8月在瑞士联邦理工大学做博士后研究工作,师从国际著名陶瓷科学家Gauckler教授。1996年8月至今,分别担任清华大学材料系讲师、副教授、教授、博导。2006年7月,被中北大学聘为特聘教授,并担任先进陶瓷实验室主任。2010年5月,被聘为大连交通大学兼职教授。2014年5月,被聘为河北工程大学兼职教授。同时,杨金龙教授担任硅酸盐学报编委,中国硅酸盐学会溶胶凝胶分会理事,材料导报编委,IJMPT(International Journal of Materials Product and Technology)Guest Editor。曾获多项荣誉,包括国家技术发明二等奖1项,河北省科技进步二等奖1项,山西省自然科学二等奖1项,其他省部级科技奖项3项,德国纽伦堡国际发明博览会金奖1项,国际发明展览会金奖1项。截至2017年12月31日,通过技术成果鉴定
Introduction In ancient times, ceramic vessels or crafts were usually manufactured using clay-based natural raw materials. It is well known that the mud mixed clay with water has good plasticity and can be easily processed into products of various shapes. However, the forming techniques used earlier were mainly manual proce-dures. Therefore, to a large extent, the forming of ceramic wares was just a kind of skill or workmanship. By the 1960s, new ceramic materials had already developed into an independent scienti.c system. At the same time, raw materials that were used to manufacture ceramics began to transition from the clay-based system to one with accurate chemistry composition. In par...
1 Aqueous Colloidal Injection Molding of Ceramics (CIMC) Based on Gelation ....................................... 1
1.1 WhatisColloidalInjectionMolding? ..................... 3
1.1.1 Colloidal Injection Molding of Ceramics (CIMC) .. .. .. . 3
1.1.2 TheFlowchartofCIMC .......................... 4
1.1.3 The Machine of Colloidal Injection Molding ofCeramics ................................... 5
1.2 Pressure-InducedForming .............................. 6
1.2.1 Effect of Hydrostatic Pressure on Solidi.cation ......... 6
1.2.2 HomogeneityoftheGreenBodies .................. 7
1.2.3 Controlling the Inner Stress in the Green Body .. .. .. .. . 7
1.3 Stor...